Demineralization Treatment Plants (DM)
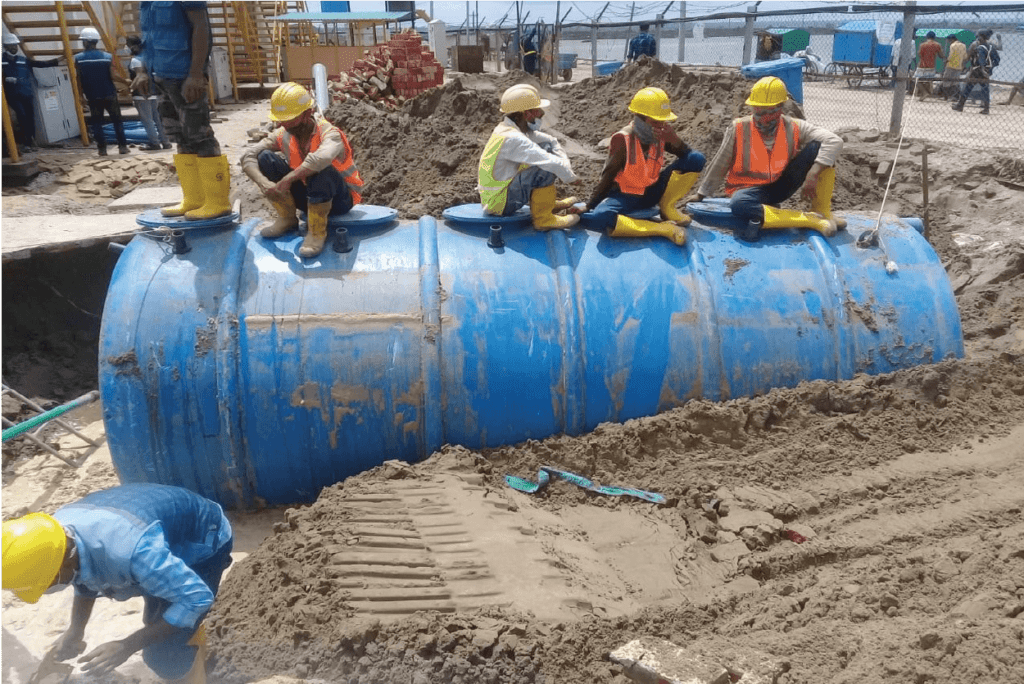
Demineralization treatment plants (DM) are facilities designed to remove dissolved minerals and impurities from water, making it suitable for various industrial applications, particularly in power generation, chemical manufacturing, and water reuse. The processes implemented in these plants can significantly affect water quality and environmental sustainability.
Water used in industries and specialized applications often requires treatment beyond typical filtration to remove dissolved salts and minerals that could disrupt processes or damage equipment. Demineralization Treatment Plants (DM) are advanced facilities designed to produce highly purified, demineralized water for industries like pharmaceuticals, power generation, electronics, and chemical production. By removing dissolved minerals, DM plants help ensure reliable, high-quality water essential for these industries.
Overview of Demineralization Processes
- Ion Exchange: This involves passing water through resin beds that exchange undesirable ions (like calcium and magnesium) with more benign ions (like sodium).
- Reverse Osmosis (RO): This technique uses a semipermeable membrane to remove a wide range of contaminants, including dissolved solids, by applying pressure to the water on one side of the membrane.
- Distillation: Water is heated to produce vapor, which is then cooled to form purified water, effectively separating it from mineral impurities.
What is a Demineralization Treatment Plant?
A Demineralization Treatment Plant (DM) is a facility that removes mineral ions—such as calcium, magnesium, sodium, chloride, sulfate, and nitrate—from water. These ions, if left untreated, can cause scaling, corrosion, and other issues in industrial machinery, negatively impacting operational efficiency and product quality. DM plants utilize ion exchange technology to effectively demineralize water, providing ultra-pure water required for high-demand applications.
Characteristics of DM Plants
- Demineralization plants can vary significantly in design and technology, depending on their purpose and scale. Key characteristics often include:
- Capacity: The volume of water treated per unit time varies based on the specific needs of the industries being serviced. For example, plants associated with power generation might handle much larger volumes than those designed for smaller applications.
- Technology Integration: Advanced technologies, such as membrane processes and biological treatments, can be implemented to improve efficiency and reduce waste generation.
- Environmental Considerations: A shift towards eco-friendly practices has encouraged the use of integrated systems that minimize freshwater consumption and reduce pollutants in wastewater.
Treatment Techniques and Strategies
- The selection of specific treatment techniques often depends on the characteristics of the wastewater being processed. Common strategies include:
- Bio-Electrochemical Systems: These systems use microbial activity to assist in the treatment process, often improving removal rates of specific contaminants.
- Natural Coagulants and Membranes: Utilizing materials such as natural coagulants alongside conventional methods aids in removing suspended solids and impurities efficiently.
- Integrated Systems: The combination of various technologies, such as physical barriers and aquatic plants, in multi-stage treatment processes can enhance overall pollutant removal capabilities.
Challenges and Future Perspectives
- Economic Factors: The financial viability of advanced technologies can constrain their widespread adoption, as initial investment costs are often high.
- Waste Management: Properly managing the residuals from demineralization processes, such as brine disposal, is critical to preventing environmental impacts.
- Regulatory Compliance: Meeting stringent environmental regulations in various regions requires continuous adaptation of technologies and processes to ensure compliance
Why are Demineralization Plants Important?
- Prevents Equipment Scaling and Corrosion: Demineralized water helps prevent the buildup of mineral deposits (scaling) that can clog pipes, boilers, and other equipment. By eliminating these minerals, DM plants reduce maintenance costs and extend the lifespan of industrial equipment.
- Ensures Product Quality: In industries like pharmaceuticals and electronics, impurities in water can compromise the quality and reliability of the final product. DM plants provide high-purity water that meets strict industry standards, safeguarding the quality and safety of products.
- Supports Operational Efficiency: Mineral-free water promotes smoother and more efficient industrial operations. For instance, power plants rely on DM water for their boilers to prevent scaling and corrosion, which enhances thermal efficiency and reduces downtime.
- Environmental Benefits: Using demineralized water decreases the need for harsh chemicals to treat scaling and corrosion, reducing the chemical footprint of industrial processes and supporting more sustainable operations.
How Do Demineralization Treatment Plants Work?
DM plants commonly use ion exchange technology to remove dissolved minerals from water. The ion exchange process typically involves two main types of resins: cationic and anionic resins. Here’s a step-by-step breakdown of the demineralization process:
- Cation Exchange: Water first flows through a cation resin bed, which removes positively charged ions like calcium (Ca²⁺), magnesium (Mg²⁺), and sodium (Na⁺). These ions are replaced with hydrogen (H⁺) ions. This process reduces the hardness of the water and prepares it for the next step.
- Anion Exchange: The water then passes through an anion resin bed, which removes negatively charged ions like chloride (Cl⁻), sulfate (SO₄²⁻), and nitrate (NO₃⁻). These ions are replaced with hydroxide (OH⁻) ions. When the hydrogen and hydroxide ions combine, they form pure water (H₂O), resulting in mineral-free, high-purity water.
- Polishing (Optional): For industries that require ultra-pure water, an additional polishing step may be added to ensure the highest purity levels, often using mixed-bed ion exchangers or advanced membrane filtration techniques.
- Regeneration: Over time, the ion exchange resins become saturated with mineral ions. To restore their effectiveness, the resins are periodically regenerated with chemical solutions, such as acids and bases, that remove the absorbed ions and allow the resins to be reused.
Key Applications of Demineralization Treatment Plants
- Power Plants: Boilers in power plants require demineralized water to prevent scaling and corrosion, ensuring efficient energy production.
- Pharmaceuticals: High-purity water is essential for pharmaceutical manufacturing to prevent contamination and ensure product safety and efficacy.
- Electronics: The electronics industry uses DM water for processes like semiconductor fabrication, where impurities can compromise component quality.
- Food and Beverage: In food processing, demineralized water helps maintain product consistency and prevents mineral interference in manufacturing processes.
Advantages of Using Demineralization Treatment Plants
- Consistent Water Quality: DM plants ensure a reliable source of mineral-free water, essential for consistent industrial performance and high-quality output.
- Cost Savings on Maintenance: By reducing scaling and corrosion, DM water minimizes maintenance costs, equipment downtime, and the need for chemical treatments, contributing to lower operational expenses.
- Enhanced Energy Efficiency: Demineralized water reduces thermal losses in boilers and other heat-exchange equipment, improving energy efficiency and lowering fuel costs.
- Environmentally Friendly: DM plants reduce the environmental impact of industrial operations by minimizing chemical usage for descaling and corrosion treatment, promoting more sustainable practices.
- Supports Regulatory Compliance: Many industries are required by regulatory bodies to use purified water to meet quality and safety standards. DM plants enable compliance with these stringent regulations, reducing the risk of penalties.
The Future of Demineralization Technology
- Advanced Membrane Filtration: Membrane-based filtration methods, such as reverse osmosis (RO), are increasingly used for demineralization due to their high efficiency and reduced chemical dependency.
- Smart Monitoring and Automation: Sensors, artificial intelligence, and data analytics can optimize water quality monitoring and automatically adjust treatment processes, improving efficiency and minimizing waste.
- Green Regeneration Methods: Traditional regeneration processes use chemicals, which can create waste. Newer, greener regeneration techniques, including electrochemical methods, are being developed to reduce chemical usage and environmental impact.
Final Thoughts
Demineralization Treatment Plants (DM) play a critical role in providing pure, mineral-free water essential for numerous industries. By removing dissolved salts and minerals, DM plants protect equipment, enhance product quality, and improve operational efficiency. With advancements in technology and a growing commitment to sustainability, DM plants are becoming more efficient, eco-friendly, and capable of meeting the increasing demands of various sectors.
As industries continue to prioritize sustainability and efficiency, DM plants will remain essential for supporting cleaner, safer, and more reliable operations.
The advancement of demineralization treatment plants is crucial for sustainable water management and environmental protection. As technologies evolve, the integration of more efficient and cost-effective methods will likely enhance the performance of these facilities, ensuring their efficacy in meeting industrial and societal needs.